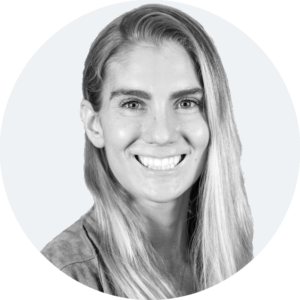
Kylie Wright
Produced Water Needs to be Managed
Produced water management in the Permian Basin (Permian) is largely reliant upon two main strategies: 1) disposal or 2) reuse in hydraulic fracturing. However, the volume of Permian produced water to be managed is so vast that if all hydraulic fracturing needs were met with reused produced water there would still be billions of barrels of water to manage each year. Currently, most of this water is disposed of in saltwater disposal wells, whose use has been complicated by induced seismicity concerns (Even the Rocks are Stressed These Days).
Other produced water management options exist, like direct discharge to surface waters or injection into aquifers for groundwater recharge, both of which require significant water treatment and have regulatory obstacles. Direct surface discharge of wastewater from oil and gas activities is currently prohibited east of the 98th meridian, and only allowed in special circumstances west of the 98th meridian, per 40 CFR part 435 Subcategory E. Although progress has been made along the path to allowing direct discharge of treated produced water to surface waters, it’s a prohibitively expensive option. Aquifer recharge is an exciting option, but the legal process and business plan are unclear, and the water must still be treated to a high standard prior to injection. The industry continues to enthusiastically endorse beneficial reuse options based on the hope that it can provide a pressure relief valve to sub-surface injection of fluids. [1]
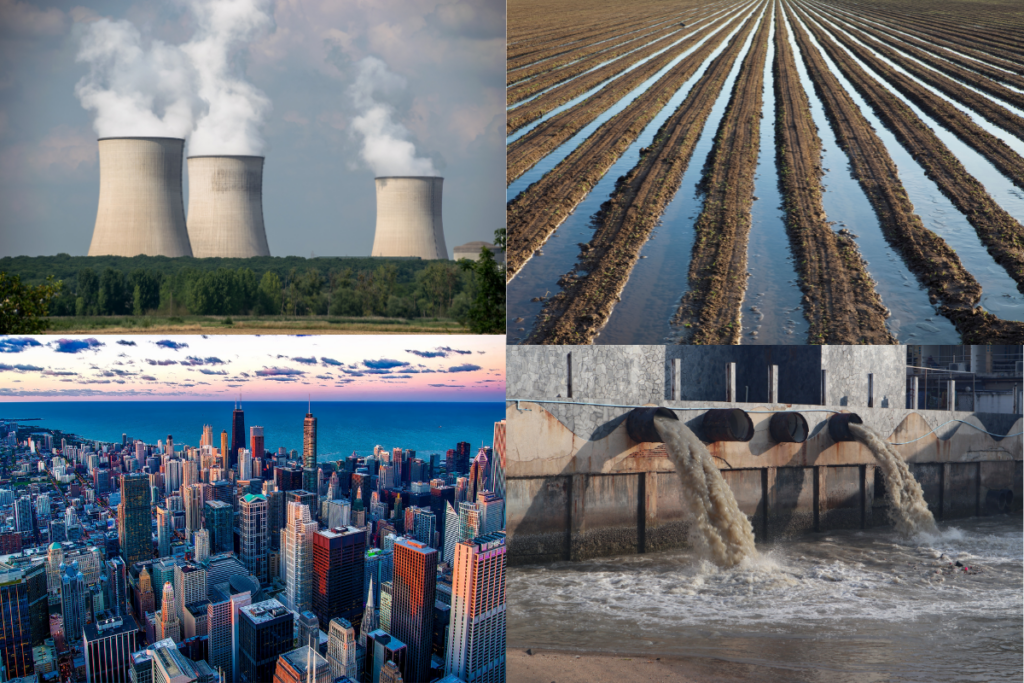
What constitutes beneficial reuse?
Beneficial reuse is a colloquial term with no exact definition. It’s frequently employed to describe the use of treated produced water outside of the oilfield for agricultural, municipal, industrial, or other uses that are not connected to the production of oil and gas. Agricultural use of produced water primarily includes the application of treated produced water in irrigation of non-edible crops like cotton. Municipal use of produced water is the transfer of treated produced water to municipal water facilities for use in, typically, non-consumption applications like sewer systems or watering systems (golf courses, houses, etc.). Beneficial reuse in industry can include use in water cooling systems or use in manufacturing processes or products. Importantly, industrial beneficial reuse could take place in downstream energy, like refining or chemicals production, which is actually considered to be a use outside of the oilfield. [2] At first blush, this would allow vertically integrated producers to streamline their beneficial water management by keeping things under one corporate umbrella.
How much water could beneficial reuse really divert from disposal?
The TX Water Development Board (TWDB) 2019 Water Use Estimates Summary indicates agricultural irrigation in TX alone uses approximately 58 billion barrels of water a year. The Permian Basin produces about 5.5 billion barrels of produced water annually. Assuming that the water could all be treated and transported to the required irrigation locations, every last drop of produced water generated in the Permian could potentially be used in TX agriculture. The assumption that all water could be treated and transported to the appropriate irrigation locations is a massive leap though, as most of this water is produced and treated in West TX and Southeastern NM, but most TX agriculture is located in the state’s northern and eastern counties. Almost any feasible end use for water, industrial, agricultural, or otherwise, necessitates reliable, consistent water flows, meaning that new infrastructure would be needed to support external reuse. [3] [4]
Water Treatment for Industrial and Agricultural Reuse
Agricultural beneficial reuse requires clearance for surface discharge of treated produced water which would inevitably require rigorous water treatment and a lengthy permitting process. Numerous studies have been underway for years to determine the water quality required by certain crops like cotton to achieve high enough crop yield, minimize treatment costs, and prevent soil or surface water contamination. These studies have made progress, but one of the primary concerns around treating produced water for surface discharge is that many of the constituents in produced water lack approved analytical techniques or toxicological information. Additional benchtop science and regulations will be needed to pave the way for produced water reuse in agriculture, which brings the timeline for this beneficial reuse option into question. Scientific determination, drafting and passing regulation, developing contracts, and building infrastructure suggests that the runway to liftoff for produced water reuse in agriculture is still years (potentially decades) into the future. Even if the water were able to be reliably, highly treated, the constituents removed from the water and left behind as waste are considered hazardous, requiring transportation to an approved hazardous solids disposal facility or injection as a slurry into the subsurface. [5] [6] [7]
Achieving highly treated produced water is currently possible with a range of proven and reliable technologies. Methods like reverse osmosis, electrodialysis, nanofiltration, mechanical vapor compression, multiple-effect distillation, capacitive deionization, and others can be deployed to treat produced water to existing surface discharge standards. However, because the existing standards fail to capture the breadth of constituents in produced water there is still general skepticism about the quality of treated produced water for discharge or use in agriculture. Additionally, these treatment technologies can increase management costs to prohibitive levels of over $1 or $2 per barrel, compared to regular reuse treatment costs of less than $1 per barrel.
Industrial beneficial reuse may be a more attainable option than agricultural or municipal reuse because the produced water may not require the same extensive degree of treatment as the other options which require treatment to a very high purity. There are already large industrial complexes relatively proximal to energy production regions that require large volumes of water, like the Tesla’s Gigafactory, Lockheed Martin’s Manufacturing facility, or numerous natural gas power plants. These facilities require significantly less water than agriculture, however. The Tesla Gigafactory, for example, is likely to require only about 12 million barrels of water a year. In 2019, the TWDB estimates that all manufacturing and power generation only used 11% of total annual water consumption across the state, or about 12.1 billion barrels of water. While this is still significantly more than produced water production, these facilities will require treated produced water to meet a highly consistent quality specification to prevent negative impacts to industrial facilities. Variation in water quality across regions may make this level of treatment and consistency challenging for operators to meet. Still, industrial reuse appears to have the strongest immediate support among industry professionals as pursuits of agricultural reuse require more time and testing.
Beneficial reuse of produced water is an admirable goal and could siphon a lot of produced water away from disposal, but there are issues to resolve. The industry has been reaching toward the brass ring of beneficial reuse for many years and has made valuable progress. However, without collective, decisive direction to move toward this goal, clarity in the regulatory space, and significant investment, beneficial reuse may remain forever on the horizon.
EMPOWERING SMART WATER MANAGEMENT
B3 Insight is building the definitive source for water data. We empower smart water management with data-driven intelligence for responsible and profitable decisions about water resources. Whatever your needs, B3 Insight’s OilfieldH2O can positively impact your water management and drilling completions – contact us at [email protected] or 720-664-8517 to learn more.